Cost of production report (CPR) – weighted average method
Definition and explanation
The cost of production report (CPR) is a document used in a process costing system that summarizes information about the flow of units and costs through the work-in-process account of a processing department. It is equal to the job cost sheet that is prepared in a job order costing system. A separate cost of production report is prepared for each processing department.
The cost of production report is considered a key management document because it provides managers with the following crucial information about the output produced and the cost incurred by a processing department:
- The number of units transferred in and transferred out by a department during the month.
- The per unit processing cost incurred by a processing department. It includes total per unit cost (i.e., total cost incurred divided by total output) as well as per unit cost for individual cost elements like direct materials, direct labor, and manufacturing overhead.
- The highest production cost(s) among materials, labor, and manufacturing overhead.
- The impact of a recent improvement in the production process on per unit cost in a processing department.
- A significant change in per unit cost due to an unexpected change in one or more cost elements like direct materials, direct labor, and manufacturing overhead.
- The hurdles or limiting factors present in one or more processing departments that could potentially disturb the overall output efficiency of the firm.
Other names used for the cost of production report are production cost report and production report.
Sections or parts of a cost of production report
A cost of production report consists of the following three sections/parts:
- Quantity schedule section
- Cost per equivalent unit section
- Cost reconciliation section
Let’s briefly describe the purpose of each section.
1. Quantity schedule section
The quantity schedule is the first section of a cost of production report. This section summarizes the flow of physical units through the relevant processing department and shows the equivalent units for materials and conversion costs. The percentage of completion of any units in work-in-process beginning and ending inventory is also shown in this section. The quantity schedule also guides the preparation of the other two sections of the cost of production report.
2. Cost per equivalent unit section
In this section, the cost per equivalent unit is computed. Under the weighted average method, it is done by dividing the total of the beginning inventory cost and the cost added during the period by the equivalent units of production computed under the weighted average method. Click here to read how equivalent units of production are computed using the weighted average method.
3. Cost reconciliation section
In this section, the cost charged to the department is reconciled or accounted for. Usually, the total cost charged to a department consists of the following:
- The cost of beginning work-in-process inventory
- The materials, labor, and overhead costs incurred by the department during the current period
- The cost transferred in from the preceding department during the period
The total of the above costs is accounted for by computing the following amounts:
- The cost of units transferred to the next department or finished goods storeroom.
- The cost of ending work-in-process inventory.
Example
XYZ Company produces a product used to clean the mirrors and head lights of vehicles. The company uses a process costing system and has two processing departments – Department X and Department Y. The processing starts in Department X, where three different chemicals are mixed together in equal proportions. After mixing in Department X, the partially complete units are transferred to Department Y. The following data has been taken from Department X.
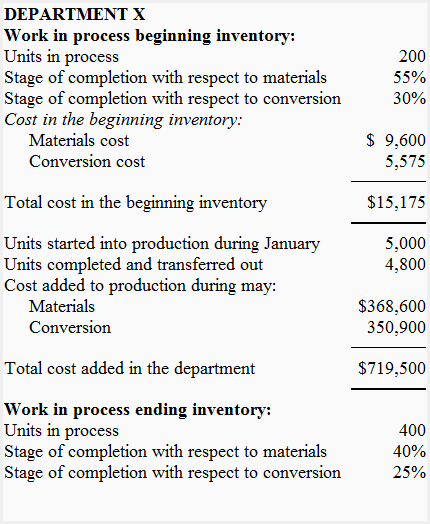
Required: Using the above data, prepare a cost of production report for department X for the month of January.
Solution
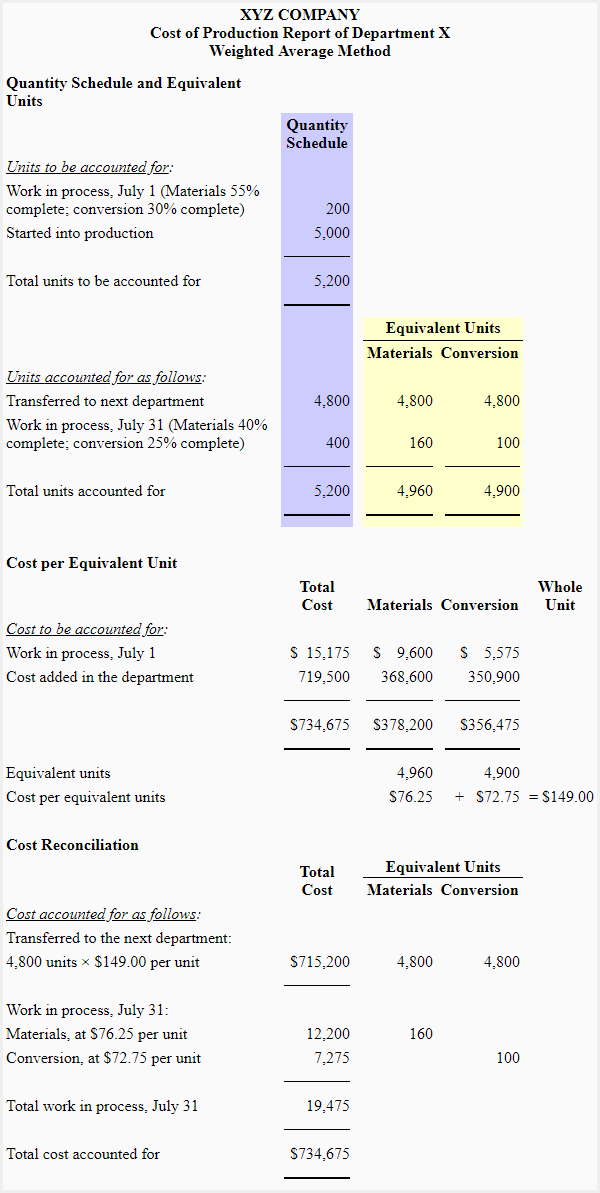
Cost of Production Report – FIFO method is missing
Kindly upload with the same pattern. Its easy to understand.
Thanks
Regards,
Good report