Process costing – normal loss or spoilage
This page explains the treatment of normal loss in a process costing system. Click here if you want to learn about the treatment of abnormal loss.
Many factors, like shrinkage, seepage, evaporation, weight loss, and the use of inefficient equipment, cause the loss or spoilage of units in processing departments. In process costing, this loss of units is categorized as normal or abnormal. This categorization is essential mainly for two reasons. Firstly, like many other costing systems, normal and abnormal losses are treated and accounted for differently in a process costing system. Secondly, this categorization is helpful in finding and fixing any abnormalities present in the production processes carried out in various departments.
Before exemplifying the treatment of normal loss, let’s briefly explain what normal loss or spoilage is in the context of process costing.
What is normal loss or spoilage in process costing?
The normal loss is the unavoidable loss of units in a processing department that occurs primarily due to the nature of the production operation or the nature of the raw materials being processed. This loss cannot be avoided in a normal and efficient production environment and is considered within the normal or acceptable tolerance limit for machines and human errors.
In many industries, the normal loss is known or highly expected, and its quantum can be estimated in advance of the start of production. Since normal loss is inherent in certain manufacturing processes, companies usually make a provision for it before starting their production process. The normal loss is sometimes referred to as standard loss.
The normal loss is not presented as a separate cost element on the cost of production report (CPR) of the relevant department. The cost of lost units is spread over the number of good units, which results in an increased per unit cost of the good output.
Treatment of normal loss in cost of production report (CPR)
Normal loss in the first department
If the normal loss occurs in the first processing department, it only increases the unit cost of the remaining good output because the total cost is divided by only the good units to obtain the per unit cost of the output. The normally lost units are not considered while computing equivalent units, which results in a decreased number of equivalent units and increased unit cost for materials, labor, and manufacturing overhead. The increased per unit cost of these three cost elements results in an increased total per unit cost in the department.
To sum up the above discussion, we can say that the normal loss in the first department is fully ignored. It is not made part of any computation while preparing the cost of production report for the first department.
Normal loss in a department subsequent to first
When normal loss occurs in a department subsequent to the first department, the per unit cost from the preceding department needs to be adjusted for the units lost in the subsequent department. It can be done using either of the two formulas given below:
Formula 1:
Lost unit cost = [Cost from preceding department ÷ Good units] – Unit cost from preceding department before adjustment
Formula 2:
Lost unit cost = (Lost units × Unit cost from preceding department before adjustment) ÷ Good units
Now consider the following example for a proper understanding of the treatment of normal loss while preparing the cost of production report for the first and subsequent departments:
Example
David Corporation produces a chemical that is processed through two separate departments – Department 1 and Department 2. For November, the following data has been taken from two departments:
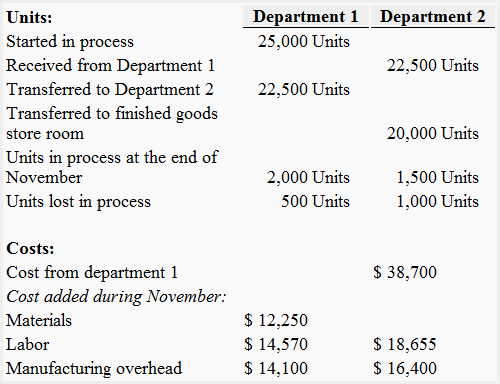
All materials are added in the 1st department at the start of the manufacturing process. The 2,000 units in the work-in-process ending inventory of the 1st department were 100% complete as to materials and 50% as to labor and manufacturing overhead costs. The 1,500 units in the work-in-process ending inventory of the 2nd department were 1/3 complete as to labor and manufacturing overhead costs. No abnormal loss was observed in any department during the month. There was no work-in-process inventory in both departments at the beginning of November.
Required: Using the data given above, prepare a separate cost of production report for the 1st and 2nd departments of David Corporation.
Solution
1. Cost of production report – 1st Department
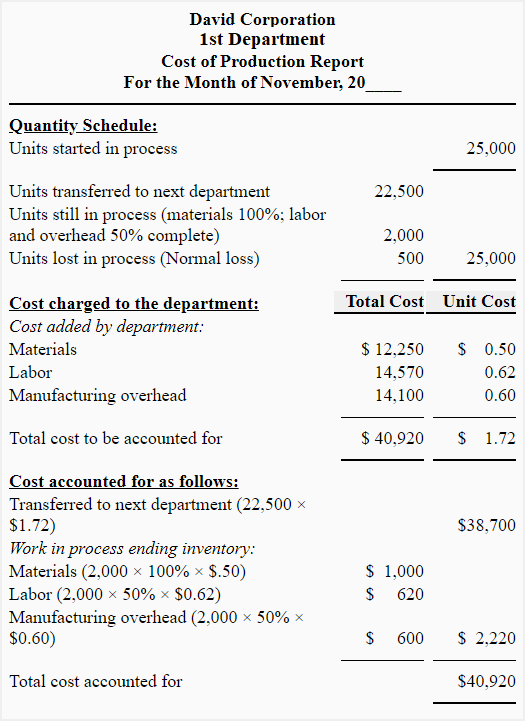
Equivalent units of production and unit cost – 1st Department:
Computation of equivalent units:
Materials: 22,500 units + 2,000 units = 24,500 units
Labor and overhead: 22,500 units + (2,000 units × 50%) = 23,500 units
Computation of unit cost:
Materials: $12,250/24,500 units = $0.50
Labor: $14,570/23,500 units = $0.62
Overhead: $14,100/23,500 units = $0.60
2. Cost of production report – 2nd Department
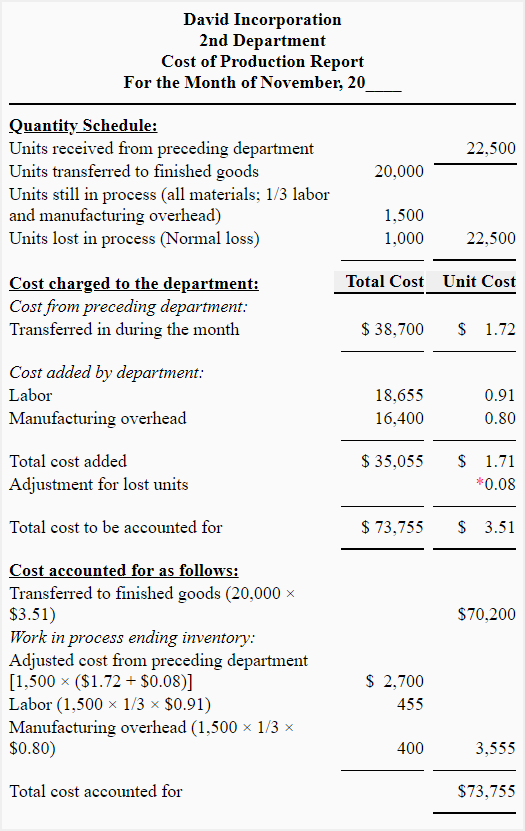
Equivalent units of production and unit cost – 2nd department
Computation of equivalent units:
Labor and overhead: 20,000 units + (1500 units × 1/3) = 20,500 units
Computation of unit cost:
Labor: $18,655/20,500 units = $0.91
Overhead: $16,400/20,500 units = $0.80
*Adjustment for lost units
In the 2nd department, the per unit cost of $1.72 transferred in from the 1st department must be adjusted for the units lost in the 2nd department. The adjustment amount is $0.08 per unit, which can be worked out using one of the following two methods:
Method 1:
[Cost from preceding department/Good units] – Unit cost from preceding department before adjustment
= [38,700/(22,500 – 1,000)] – $1.72
= $1.80 – $1.72
= $0.08
Method 2:
(Lost units × Unit cost from preceding department before adjustment)/Good units
= (1,000 × $1.72)/21,500
= $0.08
Normal loss at the end of process
In the above discussion, we have assumed that the normal loss is identified during the production process. However, a different treatment is adopted when normally lost units are identified at the end of the production process.
Where the normal loss is identified at the end of the production process, the cost of lost units is charged to units completed and transferred out during the period. In such a situation, no part of the normal loss is charged to unfinished or work-in-process ending inventory in the department.
This situation is illustrated by the following cost of production report of Department Y of Roberts Company. The normal loss is 900 units (5% of good output), which has been identified at the end of the production process.
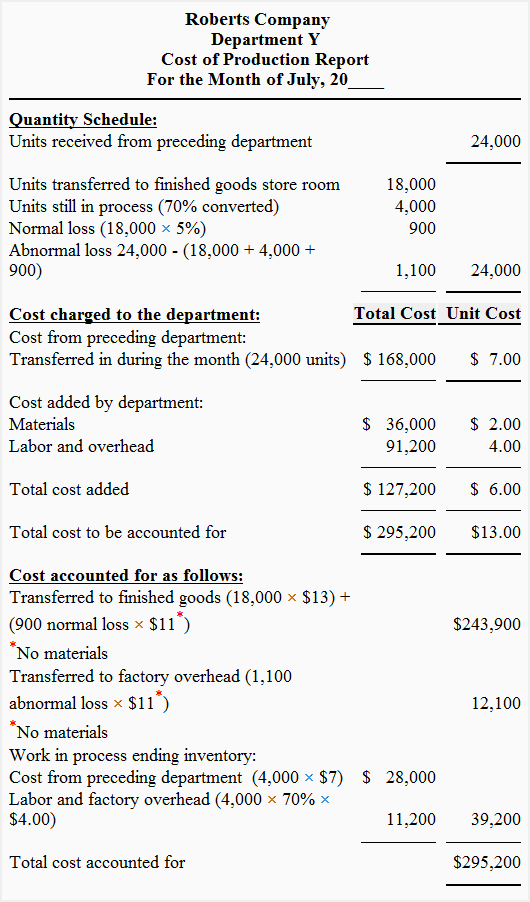
Equivalent units:
Materials: 18,000 units
Labor and overhead: 18,000 + (4,000 × 0.7) + 900 + 1,100
= 22,800 units
Unit cost:
Materials: $36,000/18,000 units = $2.00 per unit
Labor and overhead: $91,200/22,800 units = 4.00 per unit
Notice that the normal loss of 900 units identified at the end of the process has been charged to good units transferred to the finished goods store room. No part of this loss has been charged to work-in-process ending inventory.
Leave a comment